What if Your Pallet Was an Asset, Not Just a Cost?
Hidden treatment fees, excess shipping weight, and compliance risks aren't features.
They are bugs. We engineered them out.
Compressed Wood Pallets vs. Traditional Wood Pallets
The fundamental differences aren't just in wood and glue; they're in performance, cost, and your bottom line.
See how our innovative process creates a smarter logistics tool.
CWP's nestable design dramatically optimizes storage & transport costs.
Significantly lowers freight charges, especially advantageous in air cargo.
Inherently compliant with ISPM 15, no heat treatment or fumigation required.
A Tale of Two Origins: Materials & Manufacturing
The fundamental differences between the two pallet types stem from their disparate raw materials and production processes, which dictate their performance, cost, and applications.
Compressed Wood Pallet (CWP)
Molded under high heat and pressure from recycled wood fibers and resin. A prime example of the circular economy with a safe, nail-free design.
Traditional Wood Pallet
Constructed from natural softwood or hardwood lumber, assembled with nails or bolts. Strong, but with risks of splinters and protruding nails.
The Compliance Divide: ISPM 15 & The Passport to Global Trade
For international shipments, ISPM 15 compliance is decisive. The inherent exemption of CWPs creates an insurmountable advantage in export operations.
CWP Export Workflow
(High Temperature & Pressure)
Advantage: Zero treatment costs, no compliance risk, faster delivery times.
Traditional Pallet Export Workflow
(ISPM 15 Required)
(Risk of Customs Inspection)
Disadvantage: Added costs, time delays, risk of rejection or destruction.
Lifecycle Trajectories: Repairability vs. Recyclability
This fundamental difference in lifecycle models dictates their best-fit applications: one built for repairable long-term service, the other optimized for an efficient single journey.
Traditional Pallet: A Cycle of Repair
Damaged components are easily replaced, extending the pallet's life through multiple repair cycles. The backbone of closed-loop and pooling systems.
CWP: A One-Way Trip to Recycling
The one-piece structure is non-repairable. Damaged pallets are ground down and recycled into raw material for new products.
The Strategic Decision Framework: What's Your Best Move?
Business Application / Scenario | Compressed Wood Pallet (CWP) | Traditional Wood Pallet |
---|---|---|
International Export (Sea/Air) | ✓✓ Highly Recommended | ✗ Costly & Risky |
Domestic Closed-Loop / Pooling Systems | ✗ Not Recommended (Non-repairable) | ✓✓ Highly Recommended |
Food / Pharma / Hygiene-Sensitive | ✓✓ Highly Recommended | ✓ Viable (with treatment) |
Heavy-Duty Industrial / Racking | ✓ Viable (check load/compatibility) | ✓✓ Highly Recommended |
Our Competitive Technology Advantages
Three breakthrough innovations that establish compressed wood pallets' market leadership
Nestable Engineering Design
Proprietary round-foot geometry enables perfect nesting, delivering up to 75% space savings during empty transport and dramatically reducing logistics costs. Optimized specifically for export trade and long-distance shipping operations.
One-Piece Molding Technology
Advanced high-temperature, high-pressure molding process creates nail-free, adhesive-free construction that eliminates all safety hazards. Smooth surface finish ensures easy cleaning and meets the most stringent food and pharmaceutical industry standards.
Inherent Compliance Advantage
Manufacturing process naturally achieves ISPM15 compliance through thermal treatment, requiring zero additional processing for global customs clearance. 100% recyclable materials support corporate sustainability initiatives and ESG goals.
The Economic Showdown: Total Cost of Ownership (TCO)
There is no universally "cheaper" pallet. CWPs excel in one-way export scenarios, while traditional pallets are more economical in domestic closed-loop systems due to their repairability. Use our calculator to determine your optimal choice.
1. Enter Your Operational Parameters
Fleet Scale & Purchase Costs
Annual Operating Costs
Operational Savings & Export Compliance Costs (Annual)
2. Your TCO Analysis
$0
Estimated Annual Net Savings
0%
Return on Investment
N/A
Payback Period (Years)
Annual TCO Comparison
Raw Materials Excellence: Cost Foundation
Discover how we transform 'waste materials' into premium-grade pallets, achieving genuine cost advantages through circular economy principles
Mountains of quality waste materials – our 'family treasure'
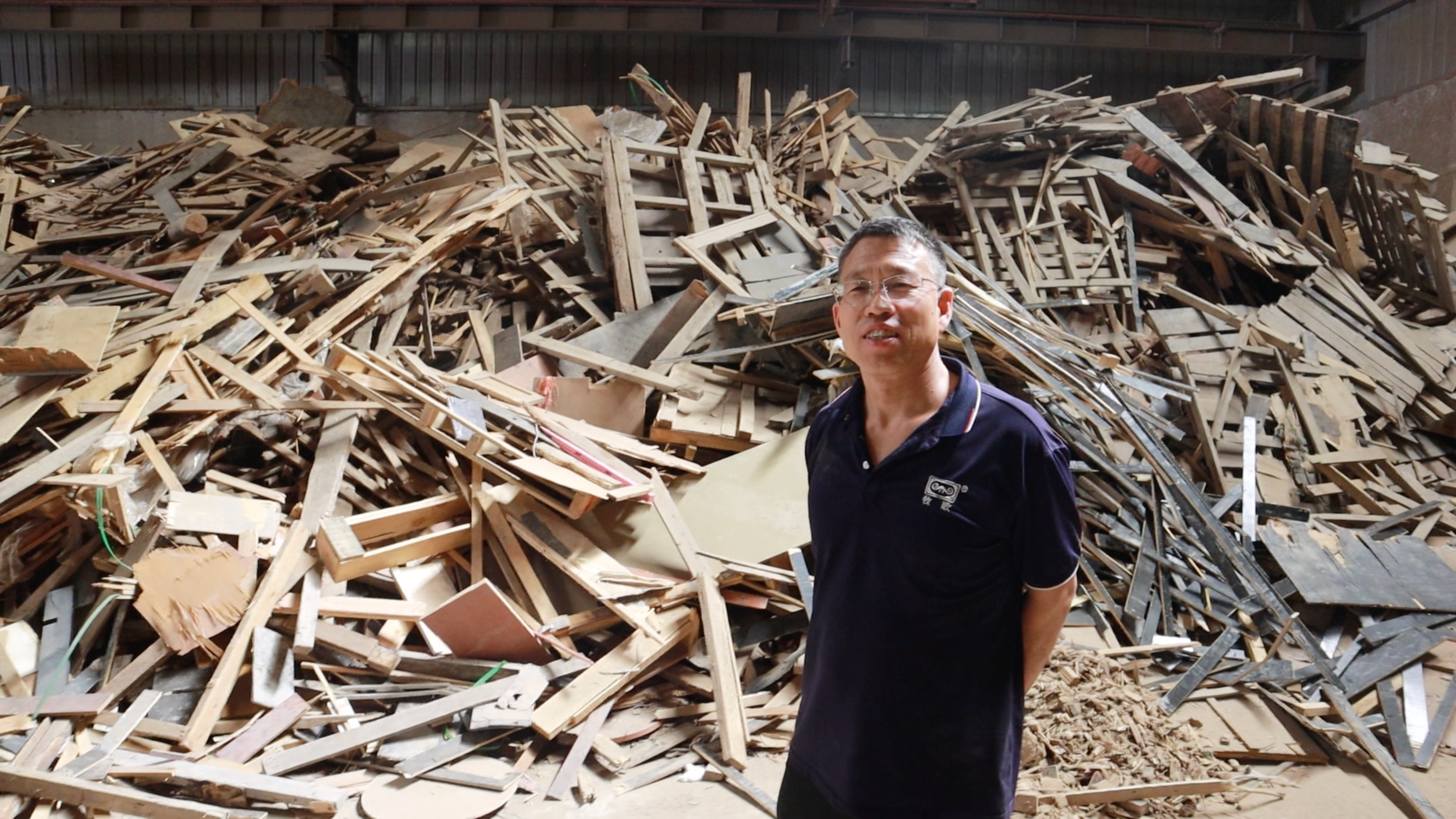
The Problem Next Door is Our Foundation
Every pallet we create begins its life somewhere else – often just a few kilometers from our factory. It might start as shavings from a furniture workshop, offcuts from a construction site, or even a retired pallet at the end of its first journey.
In Shandong, a hub of both industry and forestry, these high-quality wood byproducts are abundant. For many, they are a disposal challenge. For us, they are the first step in our engineering process.
'By transforming this 'waste' into a high-value product, we build a powerful win-win ecosystem.'
Our neighbors efficiently solve a problem, and we secure a steady stream of excellent raw materials at a fundamentally competitive cost. Our cost-effectiveness isn't a trick; it's a testament to smart, regional synergy.
Not All Fiber is Created Equal: Our Obsession with Material Quality
People think any wood scrap will do. That's not our way. We are incredibly selective. For instance, we typically avoid freshly cut, young branches because their cellulose structure isn't mature enough. The fibers are weak.
'We've learned through years of experience that wood with a longer growth cycle – fiber that has 'lived' a little – performs far better under pressure.'
This seemingly small detail makes a world of difference in the final pallet's load-bearing capacity and durability. This is the kind of deep material knowledge that spec sheets will never tell you.
— Our Chief Engineer
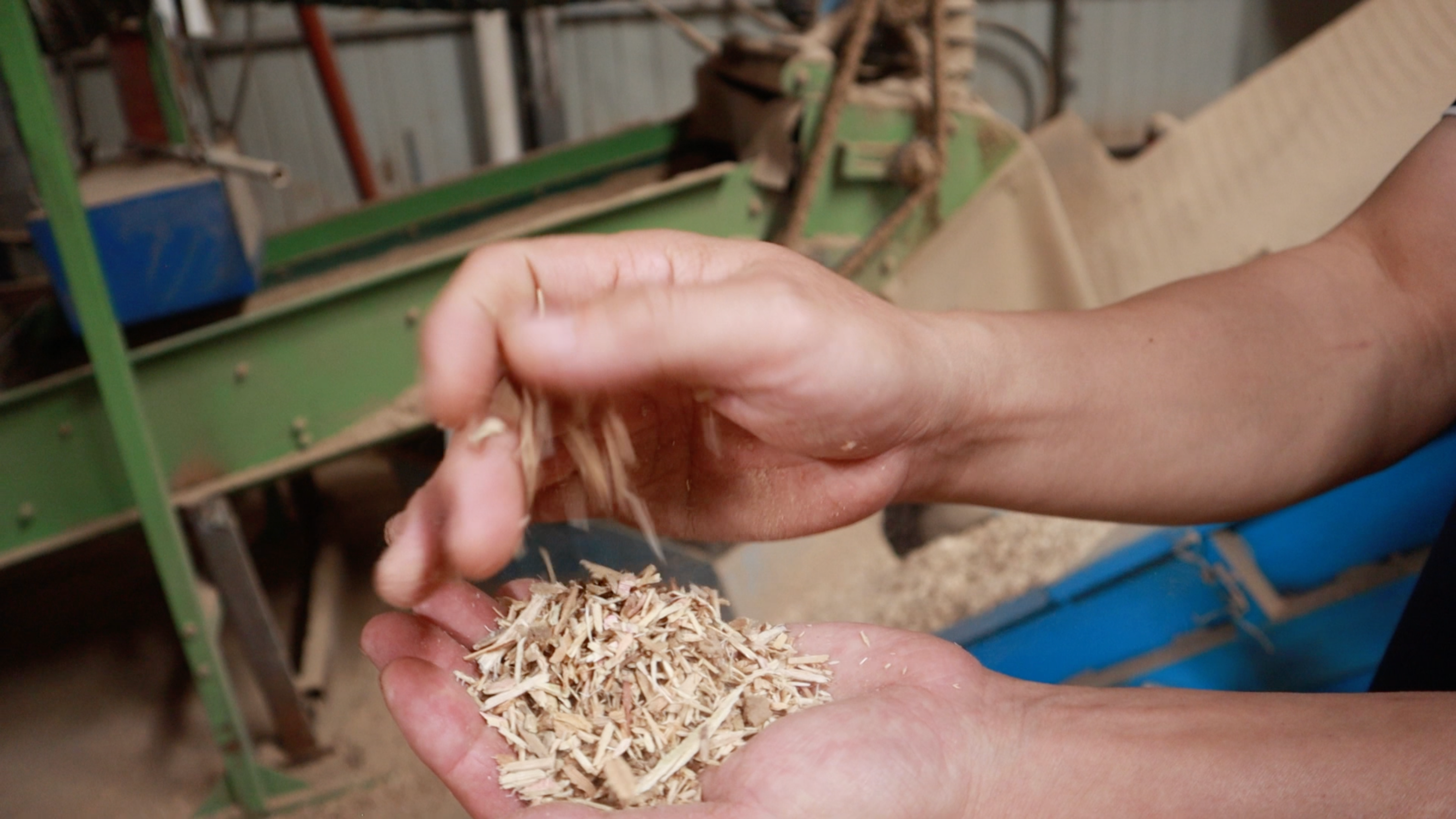
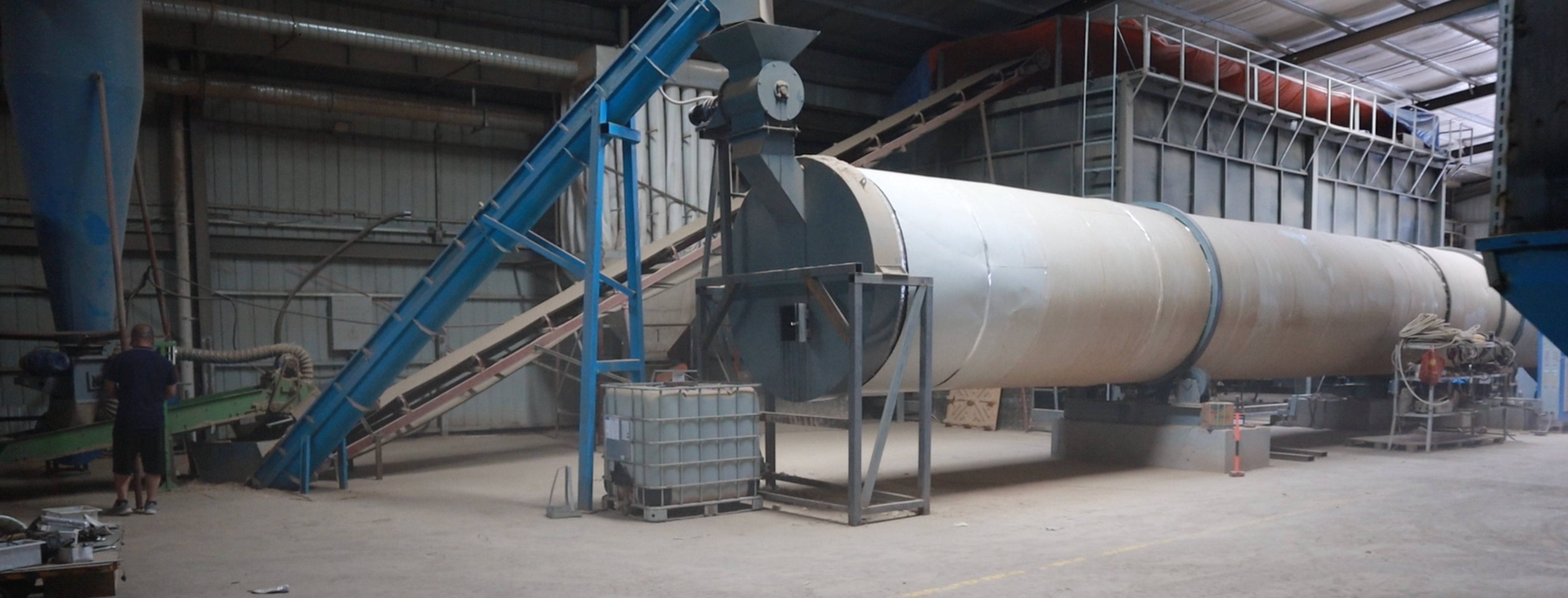
Always Prepared: How We Guarantee Supply Chain Stability
What happens if the supply of dry, recycled materials tightens during peak production? Our clients don't need to worry. We have a robust Plan B.
We are equipped with our own industrial drying kilns. This allows us to process fresh, high-quality wood materials – like sustainable forestry byproducts – pulverize them, and dry them to our exact specifications.
Full Control
Complete control over our raw material pipeline, ensuring quality standards
On-Time Delivery
Consistent demand fulfillment regardless of external market fluctuations
Your supply chain reliability is our top priority.
Raw Materials Supply Data
Stable, sustainable, high-quality material foundation
More Than a Pattern: The Engineering Behind Our Reinforcement Ribs
From manufacturer to solution designer: 20 years molded into every line
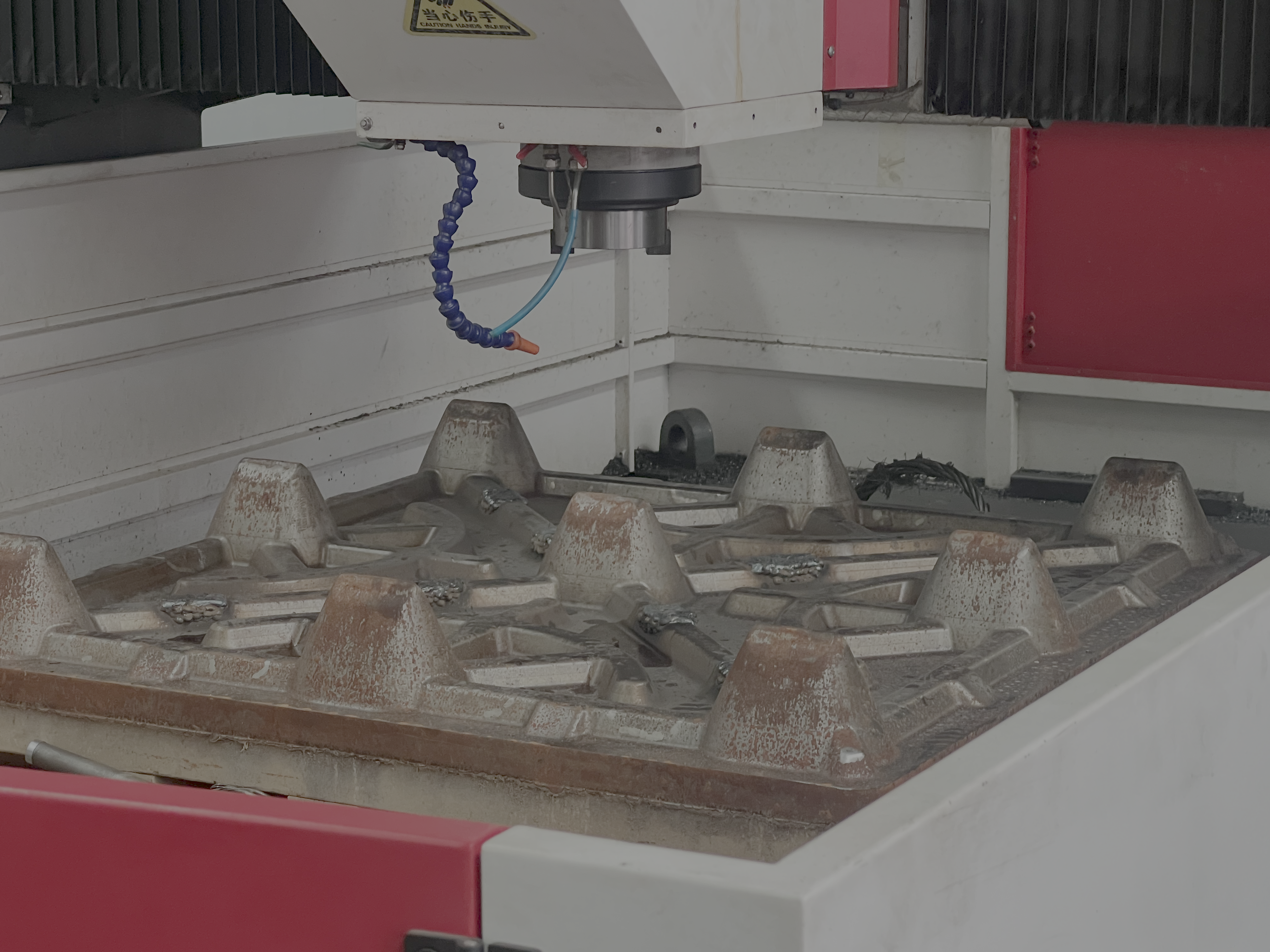
Latest Generation "Anchor" Rib Design
Every line optimized through mechanical analysis
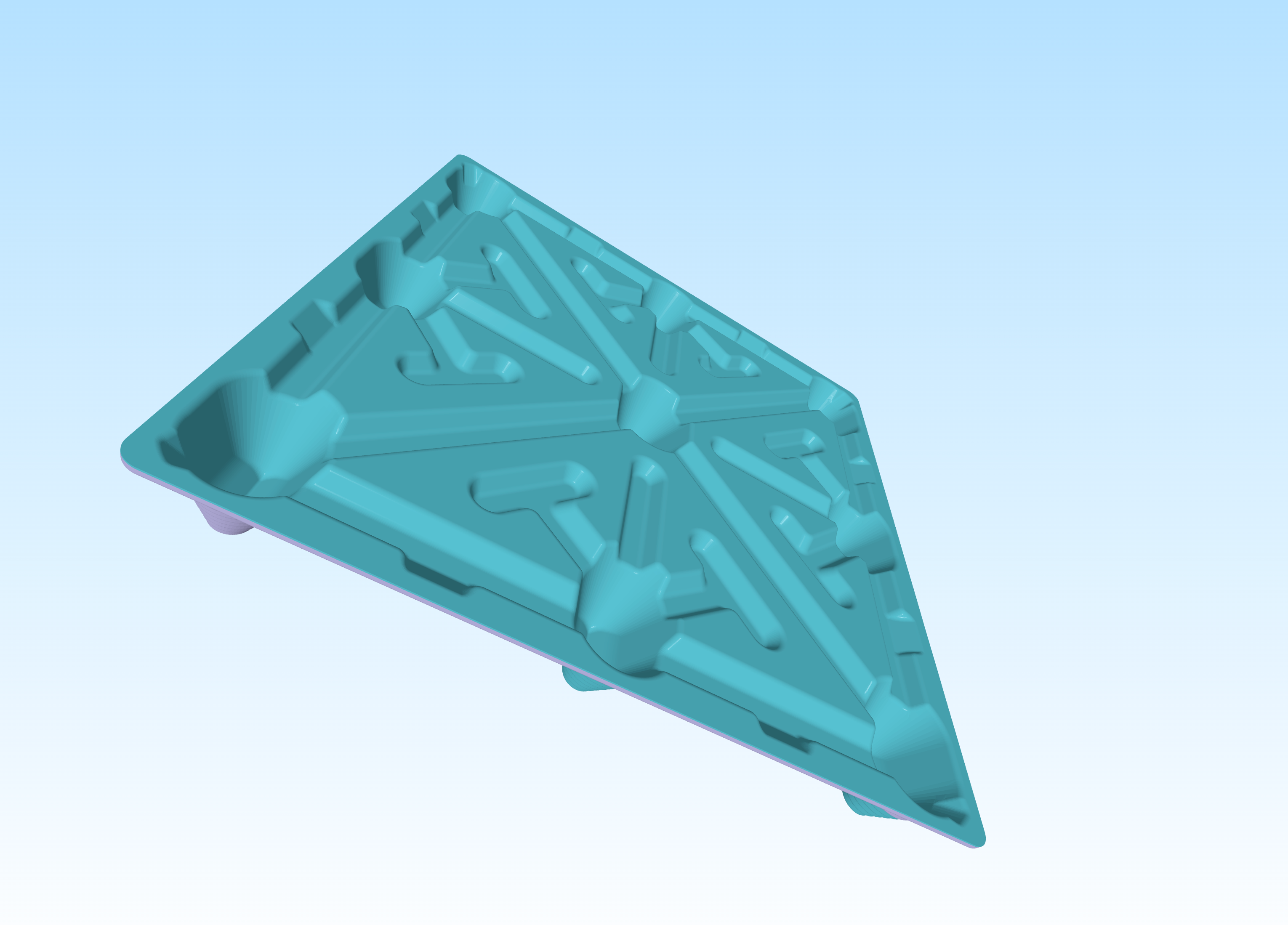
Precision CAD Modeling Design
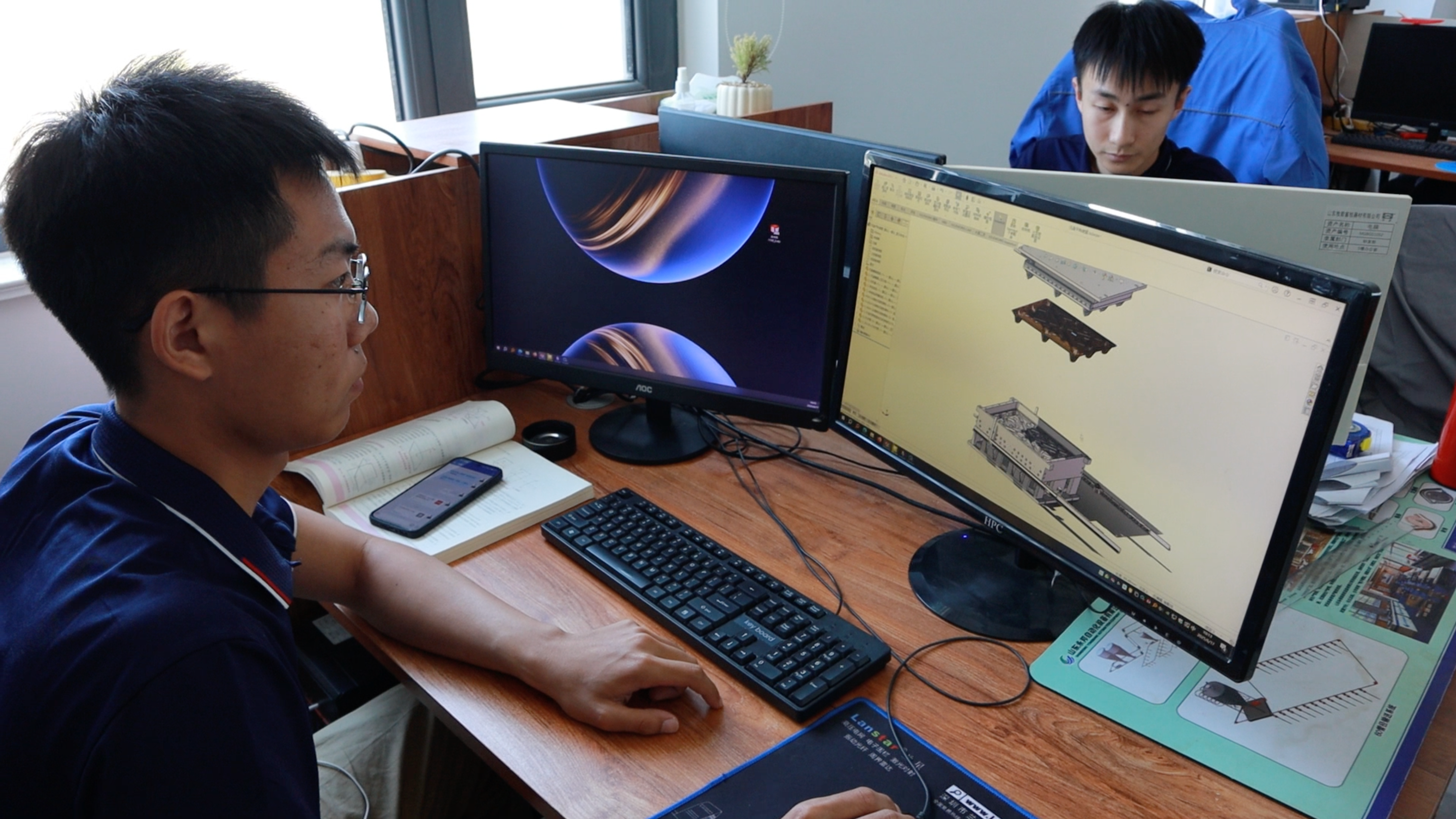
Every Line Has a Purpose. Period.
To the untrained eye, the patterns on our pallets might look like a design choice. For our engineers, they are a precise science. Each rib, each groove, each curve is the result of rigorous analysis in materials science and engineering mechanics.
Our design principle is one of **optimized performance**. We don't chase after the absolute maximum load capacity, because that leads to over-engineering and waste – a cost you shouldn't have to bear. We also never cut corners, which would compromise safety.
Our Engineering Philosophy:
We engineer our pallets to perfectly meet and exceed international standards (GB and Euro Pallet standards), providing **exactly the strength you need, without waste**. This is responsible engineering.
Evolution of Strength: Our Proprietary Rib Design
The reinforcement ribs you see on our pallets today didn't happen overnight. They are the product of **over 20 years of relentless research, development, and real-world testing.**
We started with simpler designs, like T-shaped ribs. Through countless cycles of modeling, prototyping, and load testing, we evolved our designs.
Design Evolution History
Our latest generation features a proprietary structure, inspired by the strength of "Chuan" (川) and "Tian" (田) characters from Chinese logograms, resulting in a design that masterfully distributes stress across the entire pallet.
**This unique, proprietary design is our secret to delivering exceptional strength-to-weight ratio.**
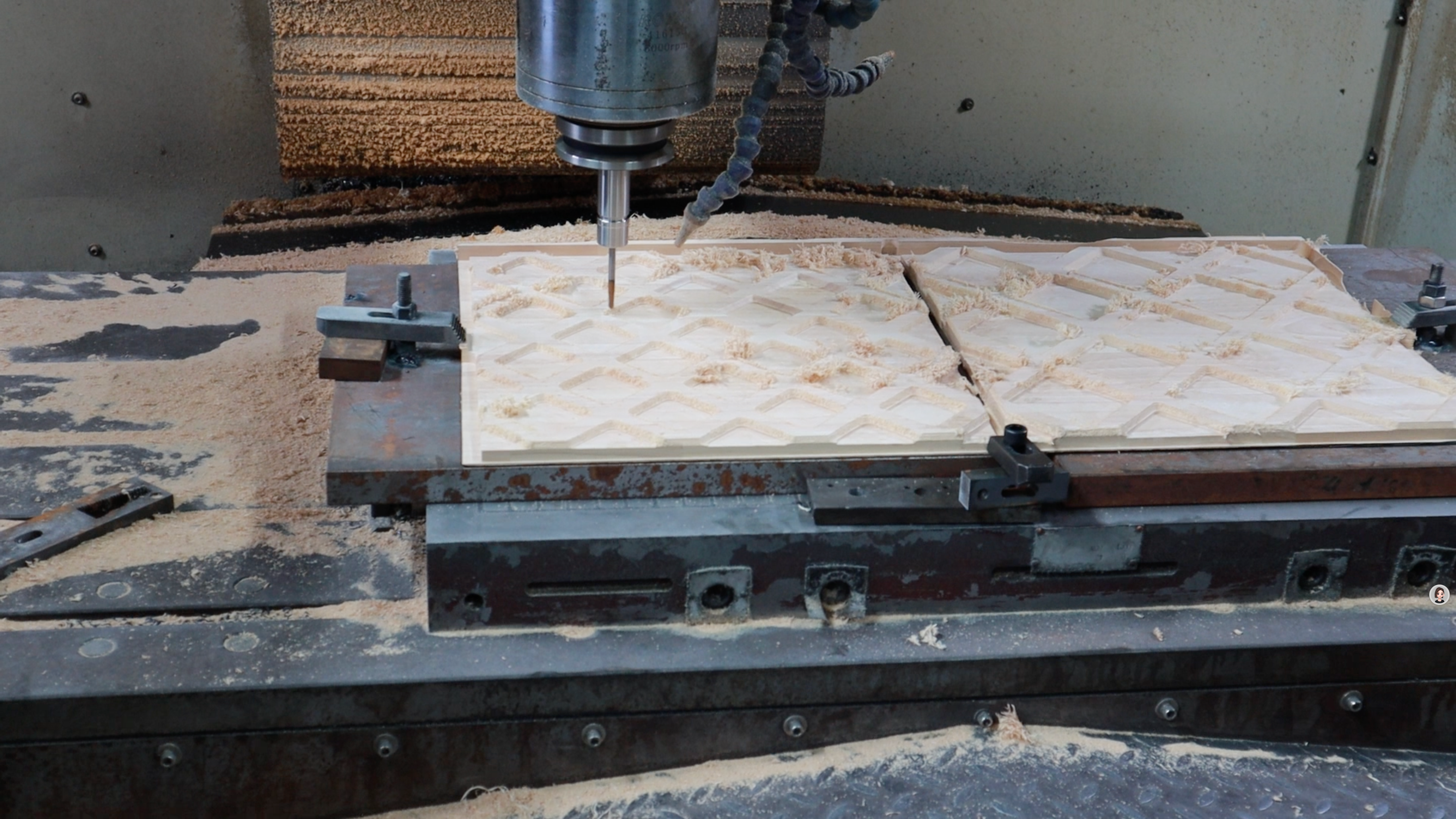
Ready to Optimize Your Supply Chain?
Connect with our technical experts to discover how compressed wood pallets can create measurable value for your logistics operations.